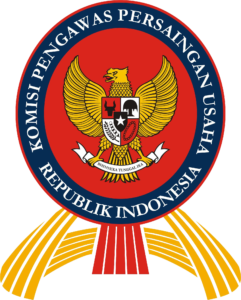
Badan Riset dan Inovasi Nasional
07-11-2022
12-08-2024
b234c013-14b6-45bf-b000-155b22f3b344
Three kinds of pulp fiber (i.e. kenaf, pineapple and coconut fiber)were characte...
Green composites were needed by automotive industries because they are environme...
The aim of this study is to evaluate the effect of cellulose fibers from oil pal...
Sweet sorghum bagasse (SSB) and citric acid (CA) were used as sustainable raw ma...
The environmental issues demand the development of environmentally friendly chem...
INFORMASI: Data berikut ini masih dalam proses pemenuhan Prinsip SDI.
Utilization of Micro Sisal Fibers as Reinforcement Agent and Polypropylene or Polylactic Acid as Polymer Matrices in Biocomposites Manufacture
Sisal (Agave sisalana) as a perennial tropical plant grows abundantly in Indonesia. Its fibers can be used as the reinforcement agent of biocomposite products. Utilization of sisal as natural fiber has some notable benefits compared to synthetic fibers, such as renewable, light in weight, and low in cost. Manufacture of biocomposite requires the use of matrix such as thermoplastic polymer, e.g. polypropylene (PP) and polylactic acid (PLA) to bond together with the reinforcement agent (e.g. sisal fibers). In relevant, experiment was conducted on biocomposites manufacture that comprised sisal fibers and PP as well as PLA. Sisal fibers were converted into pulp, then refined to micro-size fibrillated fibers such that their diameter reduced to about 10 μm, and dried in an oven. The dry microfibrillated sisal pulp fibers cellulose (MSFC) were thoroughly mixed with either PP or PLA with varying ratios of MSFC/PP as well as MSFC/PLA, and then shaped into the mat (i.e. MSFC-PP and MSFCPLA biocomposites). Two kinds of shaping was employed, i.e. hot-press molding and injection molding. In the hot-press molding, the ratio of MSFC/PP as well as MSFC/PLA ranged about 30/70-50/50. Meanwhile in the injection (employed only on assembling the MSFC-PLA biocomposite), the ratio of MSFC/PLA varied about 10/90-30/70. The resulting shaped MSFC-PP and MSFC-PLA biocomposites were then tested of its physical and mechanical properties. With the hot-press molding device, the physical and mechanical (strength) properties of MSFC-PLA biocomposite were higher than those of MSFC-PP biocomposite. The optimum ratio of MSFC/PP as well as MSFC/PLA reached concurrently at 40/60. The strengths of MSFC-PP as well as MSFCPLA biocomposites were greater than those of individual polymer (PP and PLA). With the injection molding device, only the MSFC-PLA biocomposite was formed and its strengths reached maximum at 30/70 ratio. The particular strengths (MOR and MOE) of MSFC-PLA biocomposite shaped with injection molding were lower than those with hot-press molding, both at 30/70 ratio. The overall MOR of such MSFC-PLA biocomposite was lower than that of pure PLA, while its MOE was still mostly higher. Journal of Forestry Research, Vol. 10, No. 1. Hal. 11-20